Metal injection molding

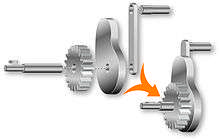
Metal injection molding (MIM) is a metalworking process by which finely-powdered metal is mixed with a measured amount of binder material to comprise a "feedstock" capable of being handled by plastic processing equipment through a process known as injection molding. The molding process allows dilated (oversized due to binder) complex parts to be shaped in a single step and in high volume. After molding, the powder-binder mixture is subjected to steps that remove the binder (debinding) and sinter densify the powders. End products are small components used in various industries and applications. The nature of MIM feedstock flow is defined by a physics called rheology.[1] Current equipment capability requires processing to stay limited to products that can be molded using typical volumes of 100 grams or less per "shot" into the mold. Rheology does allow this "shot" to be distributed into multiple cavities, thus becoming cost-effective for small, intricate, high-volume products which would otherwise be quite expensive to produce by alternate or classic methods. The variety of metals capable of implementation within MIM feedstock are broad, but mostly stainless steels, as common in powder metallurgy; they contain the same alloying constituents found in industry standards. However, oxygen is often a difficulty and is often not specified, but can be a problem for corrosion resistance. Subsequent conditioning operations are performed on the molded shape, where the binder material is removed and the metal particles are diffusion bonded and densified into the desired state with typically 15% shrinkage in each dimension.
The metal injection molding market has grown from $9 million USD in 1986, to $382 million USD in 2004 to more than $1.5 billion USD in 2015. A related technology is ceramic powder injection molding, leading to about $2 billion USD total sales. Most of the growth in recent years has been in Asia.[2]
Process

An early developer of the process during the 1970s was Dr. Raymond E. Wiech Jr., who refined MIM technology as co-founder of a California company named Parmatech, the name being condensed from the phrase "particle materials technology".[3] Wiech later patented[4] his process, and it was widely adopted for manufacturing use in the 1980s.
MIM gained recognition throughout the 1990s as improvements to subsequent conditioning processes resulted in an end product that performs similarly to or better than those made through competing processes. MIM technology improved cost efficiency through high volume production to "net-shape", negating costly, additional operations such as machining although MIM is weak in terms of tight dimensional specifications.
The process steps involve combining metal powders with polymers such as wax and polypropylene binders to produce the "feedstock" mix that is injected as a liquid into a mold using plastic injection molding machines. The molded or "green part" is cooled and ejected from the mold. Next, a portion of the binder material is removed using solvent, thermal furnaces, catalytic process, or a combination of methods. The resulting, fragile and porous (40 volume percent "air") part, is in a condition called the "brown" stage. To improve handling often the debinding and sintering are combined into a single process. Sintering heats the powder to temperatures near the melting point in a protective atmosphere furnace to densify the particles using capillary forces in a process called Sintering. MIM parts are often sintered at temperatures nearly high enough to induce partial melting in a process termed liquid phase sintering. For example, a stainless steel might be heated to 1350 to 1400 degrees Celsius). Diffusion rates are high leading to high shrinkage and densification. If performed in vacuum, it is common to reach 96-99% solid density. The end-product metal has comparable mechanical and physical properties with annealed parts made using classic metalworking methods. Post sintering heat treatments for MIM are the same as with other fabrication routes, and with high density the MIM component is compatible with the metal conditioning treatments such as plating, passivating, annealing, carburizing, nitriding, and precipitation hardening.
Applications
The window of economic advantage in metal injection molded parts lies in complexity and volume for small-size parts. MIM materials are comparable to metal formed by competing methods, and final products are used in a broad range of industrial, commercial, medical, dental, firearms, aerospace, and automotive applications. Dimensional tolerances of ±0.3% are common and machining is required for closer tolerances. MIM can produce parts where it is difficult, or even impossible, to efficiently manufacture an item through other means of fabrication. Ideally, at least 75 dimensional specifications in a component of just 25 mm maximum size and 10 g mass is best - as for example required for watch cases, cellular telephone plugs, and laptop computer hinges. Increased costs for traditional manufacturing methods inherent to part complexity, such as internal/external threads, miniaturization, or identity marking, typically do not increase the cost in a MIM operation due to the flexibility of injection molding.
Other design capabilities that can be implemented into the MIM operation include product codes, part numbers, or date stamps; parts manufactured to their net weight reducing material waste and cost; Density controlled to within 95–98%; Amalgamation of parts and Complex 3D Geometries.[5]
The ability to combine several operations into one process ensures MIM is successful in saving lead times as well as costs, providing significant benefits to manufacturers. The metal injection molding process might be a green technology due to the significant reduction in wastage compared to "traditional" manufacturing methods such as 5 axis CNC machining for example. However, some of the older operations generate toxic emissions such as formaldehyde, dispose of chlorinated solvents, and must burn off wax or other polymers, leading to greenhouse gas emissions.
There is a broad range of materials available when utilizing the MIM process. Traditional metalworking processes often involve a significant amount of material waste, which makes MIM a highly efficient option for the fabrication of complex components consisting of expensive/special alloys (cobalt-chrome, 17-4 PH stainless steel, titanium alloys and tungsten carbides).[6] MIM is a viable option when extremely thin walls specifications (i.e., 100 micrometers) are required. Additionally, EMI shielding (Electromagnetic Interference) requirements has presented unique challenges, which are being successfully attained through the utilization of specialty alloys (ASTM A753 Type 4).[7]
References
- ↑ http://www.bing.com/Dictionary/search?q=define+rheology&FORM=DTPDIA&qpvt=rheology+definition
- ↑ Subramanian, Vijay. "Metal and Ceramic Injection Molding - AVM049C". www.bccresearch.com. Retrieved 2015-05-27.
- ↑ Williams,B. "Parmatech Shapes Metals like Plastics", Metal Powder Report, Vol. 44 No.10, 1989, p675-680
- ↑ US patent number 4197118, Manufacture of Parts for Particulate material, Apr 8 1980
- ↑ http://www.cmgtechnologies.co.uk/en/metal-injection-moulding/design.htm
- ↑ http://www.beckettmim.com/materials/
- ↑ http://www.flomet.com/capabilities/emi-magnetic-shielding.php