General Electric F414
F414 | |
---|---|
![]() | |
Type | Turbofan |
National origin | United States |
Manufacturer | General Electric |
First run | May 20, 1993[1] |
Major applications | Boeing F/A-18E/F Super Hornet Saab Gripen Demo/NG HAL Tejas Mk 2 |
Developed from | General Electric F404 |
The General Electric F414 is an afterburning turbofan engine in the 22,000-pound (98 kN) thrust class produced by GE Aviation. The F414 originated from GE's widely used F404 turbofan from the McDonnell Douglas F/A-18 Hornet, enlarged and improved for use in the Boeing F/A-18E/F Super Hornet. The engine was developed from the F412 non-afterburning turbofan planned for the A-12 Avenger II, before it was canceled.
Design and development
Origins
GE evolved the F404 into the F412-GE-400 non-afterburning turbofan for the McDonnell Douglas A-12 Avenger II. After the cancellation of the A-12, the research was directed toward an engine for the F/A-18E/F Super Hornet. GE successfully pitched the F414 as a low-risk derivative of the F404, rather than a riskier new engine. In fact, the F414 engine was originally envisioned as not using any materials or processes not used in the F404, and was designed to fit in the same footprint as the F404.[2]
The F414 uses the core of the F412 and its full-authority digital engine control (FADEC), alongside the low-pressure system from the YF120 engine developed for the Advanced Tactical Fighter competition. One of the major differences between the F404 and the F414 is the fan section. The fan of the F414 is larger than that of the F404, but smaller than the fan for the F412.[3] The larger fan section increases airflow mass by 16% and is 5 inches (13 cm) longer. To keep the engine in the F404's footprint, the afterburner section was shortened by 4 in (10 cm) and the combustor shortened by 1 in (2.5 cm). Another change from the F404 is the fact that the first three stages of the high pressure compressor are blisks rather than dovetailed blades, saving 50 pounds (23 kg) in weight.[2] Furthermore, the FADEC guided F414 uses a fuel actuated "fueldraulic" system to manipulate the convergent-divergent nozzle in the afterburner section, which is a system which uses fuel from the aircraft's fuel system as hydraulic fluid, rather than relying on a separate hydraulic system with its associated fluid reservoir ("fueldraulic" systems have become popular in applications such as this, and even in more major systems in some cases).[4]
Further development
The F414 continues to be improved, both through internal GE efforts and federally funded development programs. By 2006 GE had tested an Enhanced Durability Engine (EDE) with an advanced core. The EDE engine provided a 15% thrust increase or longer life without the thrust increase. It has a six-stage high-pressure compressor (down from 7 stages in the standard F414) and an advanced high-pressure turbine.[5] The new compressor should be about 3% more efficient. The new high pressure turbine uses new materials and a new way of delivering cooling air to the blades. These changes should increase the turbine temperature capability by about 150°F (83°C).[6] The EDE is designed to have better foreign object damage resistance, and a reduced fuel burn rate.[7][8]
The EDE program continued with the testing of an advanced two stage blade-disk (blisk) fan. The first advanced fan was produced using traditional methods, but future blisk fans will be made using translational friction welding with the goal of reducing manufacturing costs.[6] GE touts that this latest variant yields either a 20% increase in thrust or threefold increase in hot-section durability over the current F414.[5] This version is called the Enhanced Performance Engine (EPE) and was partially funded through the federal Integrated High Performance Turbine Engine Technology (or IHPTET) program.[7][9]
Other possible F414 improvements include efforts to reduce engine noise by using either mechanical or fluidic chevrons and efforts to reduce emissions with a new trapped vortex combustor.[6] Chevrons would reduce engine noise by inducing mixing between the cooler, slower bypass air and the hotter, faster core exhaust air. Mechanical chevrons would come in the form of triangular cutouts (or extensions) at the end of the nozzle, resulting in a "sharktooth" pattern. Fluidic chevrons would operate by injecting differential air flows around the exhaust to achieve the same ends as the mechanical variety. A new combustor would likely aim to reduce emissions by burning a higher percentage of the oxygen, thereby reducing the amount of oxygen available to bond with nitrogen forming the pollutant NOx.
As of 2009, the F414-EDE was being developed and tested, under a United States Navy contract for a reduced specific fuel consumption (SFC) demonstrator engine.[10][11] In addition, General Electric has tested F414 engines equipped with a second low-pressure turbine stage made from ceramic matrix composites (CMC). The F414 represents the first successful use of a CMC in a rotating engine part. The tests proved CMCs are strong enough to endure the heat and rotational stress inside the turbine. The advantage CMC offers is a weight one third that of metal alloy and the ability to operate without cooling air, making the engine more aerodynamically efficient and fuel efficient. The new turbine is not yet ready for a production aircraft, however, as further design changes are needed to make it more robust.[12]
Over 1,000 F414 engines have been delivered and the engine family has totaled over 1 million flight hours by 2010.[13]
Variants
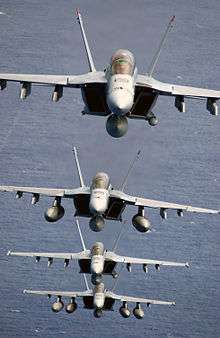
- F414-GE-400
- Flies in the Boeing F/A-18E/F Super Hornet. Also proposed for the unbuilt naval F-117N variant of the F-117 Nighthawk.[14]
- F414-EDE
- "Enhanced Durability Engine" or "EDE", includes an improved high pressure turbine (HPT) and high pressure compressor (HPC). The HPT is redesigned to withstand slightly higher temperatures and includes aerodynamic changes. The HPC has been redesigned to 6 stages, down from 7. These changes aimed at reducing SFC by 2% and component durability three times higher.[15]
- F414-EPE
- "Enhanced Performance Engine" or "EPE", includes a new core and a redesigned fan and compressor. Offers up to a 20 percent thrust boost, increasing it to 26,400 pounds (120 kN), giving an almost 11:1 thrust/weight ratio.[16]
- F414M
- Used by the EADS Mako/HEAT. Derated thrust to 12,500 lbf (55.6 kN) dry and 16,850 lbf (75 kN) wet.[17] Proposed for international versions of the Korean T-50 series of trainers and fighter aircraft, but later superseded by a new offer with a standard F414.[5][18]
- F414G
- Produced for the Saab JAS 39 Gripen Demonstrator. Slightly modified for use in a single engine Gripen, instead of a twin-engine aircraft like the F/A-18. With it, the Gripen Demonstrator reached Mach 1.2 in supercruise (without afterburner).[19]
- F414BJ
- Proposed for the Dassault Falcon SSBJ. Would produce around 12,000 lbf (53 kN) of thrust without use of afterburner.[20][21]
- F414-GE-INS6
- India's Aeronautical Development Agency selected the F414-GE-INS6 to power the HAL Tejas Light Combat Aircraft (LCA) Mk II for the Indian Air Force. India ordered 99 engines in October 2010. It produces more thrust than previous versions, and features a Full Authority Digital Electronic Control (FADEC) system.[22] The engines are to be delivered by 2013.[23]
- F414-GE-39E
- New version of the F414G for the Saab JAS-39E/F Gripen.[24]
Applications
Specifications (F414-400)
Data from General Electric[25]
General characteristics
- Type: Afterburning turbofan
- Length: 154 in (391 cm)
- Diameter: 35 in (89 cm)
- Dry weight: 2,445 lb (1,110 kg) max weight[26]
Components
- Compressor: Axial compressor with 3 fan and 7 compressor stages
- Combustors: annular
- Turbine: 1 low-pressure and 1 high-pressure stage
Performance
- Maximum thrust:
- 13,000 lbf (57.8 kN) military thrust
- 22,000 lbf (97.9 kN) with afterburner
- Overall pressure ratio: 30:1
- Thrust-to-weight ratio: 9:1[27]
- air mass flow: 77.1 kg/s
See also
- Related development
- Comparable engines
- Related lists
References
- ↑ "GE marks F414 progress; endurance tests near" (1993). Aviation Week and Space Technology. Vol. 139, No. 1; p. 31
- 1 2 "Confident GE heads to F414 CDR next month" (1994). Aerospace Daily. Vol 169, No. 34; p. 270.
- ↑ "GE wins F-18E/F study" (1991). Flight International. 4 September 1991.
- ↑ Kandebo, Stanley (1992). "GE Component Test Program to Reduce Risk in F414 Engine Development". Aviation Week and Space Technology. Vol. 136, No. 26; p. 64.
- 1 2 3 "GE F110 and F404/F414 Fighter Engines Expand Capability and Global Presence". GE Aviation, July 17, 2006
- 1 2 3 Kandebo, Stanley W. "Enhanced F414 Readies for Tests" (2004). Aviation Week and Space Technology. Vol. 160, No. 1; p. 58.
- 1 2 Norris, Guy. "GE Eyes More Powerful Engine For Super Hornets, Growlers". Aviation Week, 14 May 2009.
- ↑ Trimble, Stephen. "Boeing's Super Hornet seeks export sale to launch 20% thrust upgrade". Flight International, 12 May 2009.
- ↑ "F414 Growth Demonstrator Engine Completes Testing" (press release). GE. 12 December 2006. Retrieved 13 Aug 2009.
- ↑ "New Orders, Tech Insertions Mark Increased GE Fighter Engine Presence". GE Press Release. June 15, 2009. Retrieved 13 Aug 2009.
- ↑ "Recovery: Specific Fuel Consumption Reduction Demonstration". Federal Business Opportunities. 2009. Solicitation Number: N00019-09-G-0009. Retrieved 13 August 2009.
- ↑ Norris, Guy. "CMCs advance", Aviation Week & Space Technology, February 2–15, 2015, p. 28.
- ↑ "Proven Experience, Program Upgrades Spark GE F110 and F404/414 Popularity". GE Aviation, July 19, 2010.
- ↑ Morrocco, John (1994). "Lockheed returns to Navy with new F-117N design". Aviation Week and Space Technology. Vol. 140, No. 10; p. 26.
- ↑ "GE bids for enhanced F414 EDE funding by 2003". Flight International. 8–14 May 2001, p. 26.
- ↑ Sweetman, Bill. "GE Brings Good Things To Hornet, Gripen". Aviation Week Ares Blog, 21 April 2011.
- ↑ "Military training: Phase III". Flight International. 15 July 2003. p. 40.
- ↑ "Lockheed ponders T-50 re-engining for T-X programme". Flight global. May 24, 2011.
- ↑ Hoyle, Craig (22 January 2009). "Saab celebrates 'supercruise' test success for Gripen Demo". Flight global. Flight International..
- ↑ "Dassault officials say three-engine SST would have a 4 000-mile range" (1998). The Weekly of Business Aviation. Vol. 66, No. 22; p. 239.
- ↑ Warwick, Graham (8 September 1998). "Big-jet business". Flight global. Flight International.
- 1 2 Hoyle, Craig. "India picks GE's F414 for Tejas MkII fighter". Flight International, 1 October 2010.
- ↑ "Tejas, India's Light Combat Aircraft, History". tejas.gov.in.
- ↑ "Military engines, The F414 Engine". GE aviation.
- ↑ "Comparison Chart — Military Turbofans". GE Aviation.
- ↑ "Fighter aircraft engines, F414 GE 400". Dégel.
- ↑ "Military aircraft systems, F414". Global security.
External links
![]() |
Wikimedia Commons has media related to General Electric F414. |