Tin ceiling

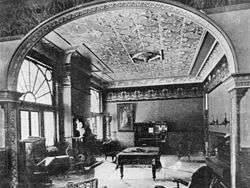
A tin ceiling is an architectural element, consisting of a ceiling finished with plates of tin with designs pressed into them, that was very popular in Victorian buildings in North America in the late 19th and early 20th century.[1] They were also popular in Australia where they were commonly known as pressed metal ceilings or Wunderlich ceilings (after the main Australian manufacturer Wunderlich).[2] They were also used in South Africa.[3]
History
Tin ceilings were introduced to North America as an affordable alternative to the exquisite plasterwork used in European homes. They gained popularity in the late 1800s as Americans sought sophisticated interior design. Durable, lightweight and fireproof, tin ceilings were appealing to home and business owners alike as a functionally attractive design element that was readily available.
It was during the late Victorian era that thin rolled tin-plate was being mass-produced. Between 1890 and 1930, approximately forty-five companies in the United States marketed metal ceilings; most were in Ohio, Pennsylvania, and New York, located along railroad lines that served as the main routes for delivering the pressed metal products directly to contractors. Sheets of tin were stamped one at a time using rope drop hammers and cast iron molds. Using this method of production, metal was sandwiched between two interlocking tools.
The top tool, or "ram," was lifted up by a rope or chain, then dropped down onto the bottom die, smashing into the metal that was underneath and permanently embedding intricate patterns into the tin. Tin ceilings were traditionally painted white to give the appearance of hand-carved or molded plaster. They were incorporated into residential living rooms and parlors as well as commercial businesses, where painted tin was often used as wainscoting.
In the 1930s, tin ceilings began to lose their popularity and ceilings as a design element were ignored. In the 21st century, some renewed interest has been shown in tin ceilings. Several companies offer conventional tin ceilings as well as panels made to fit into a drop-ceiling grid.
Restoration
Tin ceilings were built to last, and in the absence of prolonged moisture damage leading to corrosion, they usually did; however, the wear and tear over the hundred years since the heyday of tin has led to a burgeoning restoration industry. Environmental hazards from the lead paint used on turn of the century tin ceilings mean that this is a job for experts in the field.
Often restoration is achieved by simply stripping old paint, treating the metal with a protective base coat, patching minor damaged areas, and repainting. In some cases, where small sections of a ceiling have been damaged, partial restoration is needed. If a ceiling requires replacement panels, they can be easily installed if currently manufactured. If, however, a ceiling requires a historic pattern that is no longer in production, good quality panels from the existing ceiling may be used to create a mold and new customized tin can be pressed.
If full restoration is needed, meaning no part of the existing ceiling remains structurally sound, a professional can help design a new ceiling appropriate for the period and structure using existing molds or creating reproductions based on photographic evidence or architectural drawings. This latter method can be extremely expensive, and is not cost effective, due to the cost of making a custom mold for the panel and usually the metal trim that was also used with the original project.
Modern adaptation
Several companies now offer hand-painted finishes for metalwork, as well as a more permanent look that can be achieved with powder-coated finishes. For the low end of the market, imitation panels are pressed from plastic or aluminum. Tin is now fashionably used for art work, back splashes, cabinet faces, wainscoting and much more. For over 100 years the tin panel was made with nail rails around the outside of the panel, designed to overlap each other. Panels were nailed into wood furring strips which were prevalent prior to the invention of plywood. Today, nail up panels can be easily brad nailed or hand nailed, into plywood without the need for the original 1-by-2-inch (25 mm × 51 mm) furring strips. There is also a patented interlocking tin panel that will screw directly into existing drywall/popcorn/plaster ceilings, without the need for extensive plywood installation. Tin panels today are made in 24-by-24-inch (610 mm × 610 mm) and 24-by-48-inch (610 mm × 1,220 mm) sizes for easier handling and one-person installation. Today, most tin ceiling manufacturers actually use recycled blackplate steel in a thickness of only .010 or 1/100th of an inch. There are some manufacturers who also use actual tin plated steel, which is simply the blackplate steel with a thin coating of bright tin plate adhered to the base metal. Other manufacturers utilize aluminum, as it is rustproof and will last a lifetime.
This finish is also an option with dropped ceilings.
References
- ↑ "Shoptalk: Pressed Tin Ceiling". Treanor Architects. Retrieved 2015-09-18.
- ↑ "History - Wunderlite Reproduction Panels". www.wunderlite.com.au. Retrieved 2015-10-06.
- ↑ "History of tin ceilings". Retrieved 6 October 2015.
External links
Media related to Pressed tin ceilings at Wikimedia Commons