Thermographic inspection
Thermographic inspection refers to the nondestructive testing of parts, materials or systems through the imaging of the thermal patterns at the object's surface.[1] Strictly speaking, the term thermography alone, refers to all thermographic inspection techniques regardless of the physical phenomena used to monitor the thermal changes. For instance, the application of a temperature sensitive coating to a surface in order to measure its temperature is a thermographic inspection contact technique based on heat conduction where there is no infrared sensor involved. Infrared thermography on the other hand, is a nondestructive, nonintrusive, noncontact mapping of thermal patterns or "thermograms", on the surface of objects [2] through the use of some kind of infrared detector.
In addition, there are two approaches in thermographic inspection: (1) passive, in which the features of interest are naturally at a higher or lower temperature than the background, for example: the surveillance of people on a scene; and (2) active, in which an energy source is required to produce a thermal contrast between the feature of interest and the background, for example: an aircraft part with internal flaws.
When compared with other classical nondestructive testing techniques such as ultrasonic testing or radiographic testing, thermographic inspection is safe, nonintrusive and noncontact, allowing the detection of relatively shallow subsurface defects (a few millimeters in depth) under large surfaces (typically 30x30 cm2 at once, although inspection of larger surfaces is possible) and in a fast manner (from a fraction of a second to a few minutes depending in the configuration, see below).
There are many other terms widely used all referring to infrared thermography, the adoption of one or other term depends on the author’s background and preferences. For instance, video thermography and thermal imaging draw attention to the fact that a sequence of images is acquired and is possible to see it as a movie. Pulse-echo thermography and thermal wave imaging[3][4][5][6] are adopted to emphasize the wave nature of heat. Pulsed video thermography,[7][8] transient thermography,[9][10][11] and flash thermography[12] are used when the specimen is stimulated using a short energy pulse.
Techniques
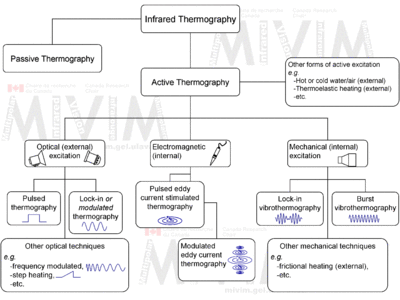
A wide variety of energy sources can be used to induce a thermal contrast between defective and non-defective zones that can be divided in external, if the energy is delivered to the surface and then propagated through the material until it encounters a flaw; or internal, if the energy is injected into the specimen in order to stimulate exclusively the defects. Typically, external excitation is performed with optical devices such as photographic flashes (for heat pulsed stimulation) or halogen lamps (for periodic heating), whereas internal excitation can be achieved by means of mechanical oscillations, with a sonic or ultrasonic transducer [13] for both burst and amplitude modulated stimulation. As depicted in the figure, there are three classical active thermographic techniques based on these two excitation modes: lock-in (or modulated) thermography and pulsed thermography, which are optical techniques applied externally; and vibrothermography,[14] which uses ultrasonic waves (amplitude modulated or pulses) to excite internal features. In vibrothermography, an external mechanical energy source induces a temperature difference between the defective and non-defective areas of the object. In this case, the temperature difference is the main factor that causes the emission of a broad electromagnetic spectrum of infrared radiation, which is not visible to the human eye. The locations of the defects can then be detected by infrared cameras through the process of mapping temperature distribution on the surface of the object.[14]
See also
- Infrared vision
- Infrared thermography
- Infrared camera
- Infrared detector
- Infrared Non-Destructive Testing
References
- ↑ http://ashtead-technology.com/productgroup/instruments/772/
- ↑ Maldague X. P. V., Jones T. S., Kaplan H., Marinetti S. and Prystay M. “Chapter 2: Fundamentals of Infrared and Thermal Testing: Part 1. Principles of Infrared and Thermal Testing,” in Nondestructive Handbook, Infrared and Thermal Testing, Volume 3, X. Maldague technical ed., P. O. Moore ed., 3rd edition, Columbus, Ohio, ASNT Press, 2001, 718 p.
- ↑ Favro L. D. and Han X. 1998, “Thermal Wave Materials Characterization and Thermal Wave Imaging,” in Birnbaum G., Auld B. A. (eds.): Sensing for Materials Characterization, Processing and Manufacturing, ASNT TONES, 1:399-415.
- ↑ Han X., Favro L. D., Kuo P. K. and Thomas R. L. 1996, “Early-Time Pulse-Echo Thermal Wave Imaging,” in D. O. Thompson and D. E. Chimenti (ed.): Review of Progress in Quantitative Nondestructive Evaluation, 15:519-524.
- ↑ Favro L. D., Han X., Wang Y., Kuo P. K. and Thomas R. L. 1995, “Pulse-echo thermal wave imaging,” in Review of Progress in Quantitative Nondestructive Evaluation, D.O. Thompson and D.E. Chimenti (ed.), 14:425-429.
- ↑ Favro L. D., Han X, Kuo P. K. and Thomas R. L. 1995, “Imaging the early time behavior of reflected thermal wave pulses,” Proc. SPIE, Thermosense XVII, 2473:162-166.
- ↑ Milne J. M. and Reynolds W. N. 1984, “The Non-Destructive Evaluation of Composites and other Materials by Thermal Pulse Video Thermography,” Proc. SPIE, Thermosense VII, 520: 119-122.
- ↑ Reynolds W. N. 1986, “Thermographic Methods Applied to Industrial Materials,” Can. J. Phys., 64: 1150-1154.
- ↑ Almond D. P. and Lau S. K. 1994, “Defect Sizing by Transient Thermography I: An analytical Treatment,” J. Phys. D: Appl. Phys., 27: 1063-1069.
- ↑ Almond D. P. and Lau S. K. 1993, “Edge Effects and a Method of Defect Sizing by Transient Thermography,” Appl. Phys. Lett., 62(25): 3369-3371.
- ↑ Saintey M. B. and Almond D. P. 1995, “Defect Sizing by Transient Thermography II: A Numerical Treatment,” J. Phys. D: Appl. Phys., 28: 2539-2546.
- ↑ Parker W. J., Jenkins R. J., Butler C. P. and Abbott G. L. 1961, “Flash Method of Determining Thermal Diffussivity, Heat Capacity, and Thermal Conductivity,” J. Appl. Phys., 32(9):1679-1684.
- ↑ Renshaw J., Chen J. C., Holland S. D., and Thompson R. B. 2011, “The sources of heat generation in vibrothermography,” NDT&E International, 44(8): 736-739.
- 1 2 Parvasi, Seyed Mohammad; Xu, Changhang; Kong, Qingzhao; Song, Gangbing (3 April 2016). "Detection of multiple thin surface cracks using vibrothermography with low-power piezoceramic-based ultrasonic actuator—a numerical study with experimental verification". Smart Materials and Structures. 25 (5): 055042. doi:10.1088/0964-1726/25/5/055042. ISSN 0964-1726.
External links
![]() |
Wikimedia Commons has media related to Thermography. |
- Canada Research Chair in Multipolar Infrared Vision – MiViM
- Active thermography and IR non-destructive testing, University of West Bohemia, New Technologies - Research Centre, department Thermomechanics of Technological Processes