Aeroshell
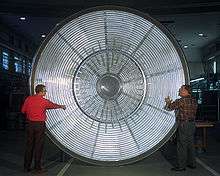
An aeroshell is a rigid heat-shielded shell that helps decelerate and protects a spacecraft vehicle from pressure, heat, and possible debris created by drag during atmospheric entry (see blunt body theory). Its main components consist of a heat shield (the forebody) and a back shell. The heat shield absorbs heat caused by air compression in front of the spacecraft during its atmospheric entry. The back shell carries the load being delivered, along with important components such as a parachute, rocket engines, and monitoring electronics like an inertial measurement unit that monitors the orientation of the shell during parachute-slowed descent.
Its purpose is used during the EDL process of a spacecraft's mission, or the Entry, Descent, and Landing process. First, the aeroshell decelerates the spacecraft as it penetrates the planet’s atmosphere. The heat shield absorbs the resulting friction. During descent, the parachute is deployed and the heat shield is detached. Rockets located at the back shell are initiated to assist in the decrease of the spacecraft's descent. Airbags are also inflated to cushion the impact. The spacecraft bounces on the planet’s surface directly after the first impact. The spacecraft's lander petals are deployed after the airbags are deflated and retracted. Communication throughout this entire process is relayed back and forth from mission control and the actual spacecraft through low-gain antennas that are attached to the back shell and on itself. Throughout the entry, descent, and landing stages, tones are sent back to earth in order to communicate the success or failure of each of these critical steps.[1]
Aeroshells are a key component of space probes that must land intact on the surface of any object with an atmosphere. They have been used on all missions returning payloads to the Earth (if one counts the Space Shuttle thermal protection system as an aeroshell). They are also used for all landing missions to Mars, Venus, Titan and (in the most extreme case) the Galileo probe to Jupiter.
Components
The aeroshell consists of two main components: the heat shield, or forebody, which is located at the front of the aeroshell, and the back shell, which is located at the back of the aeroshell. The heat shield of the aeroshell faces flow during a spacecraft's atmospheric penetration, allowing it to absorb the high aerodynamic heat caused from the entry. The backshell acts as a finalizer for the encapsulation of the payload. The backshell contains the parachute, electronics and batteries that control pyrotechnic devices, a Litton LN-200 Inertial Measurement Unit, Rocket Assisted Descent rockets, and the Transverse Impulse Rocket System. The parachute is located at the apex of the back shell and slows the spacecraft during entry, descent, and landing. The pyrotechnic control system releases devices such as nuts, rockets, and the parachute mortor. The Inertial Measurement Unit reports the orientation of the back shell while it is swaying underneath the parachute. Rocket Assisted Descent rockets provide approximately one ton of force within 2 seconds, assisting in the descent of the spacecraft vehicle. The Transverse Impulse Rocket System provides horizontal force to the back shell which helps orient it to a more vertical position during the main Rocket Assisted Descent rocket burn.
Design factors
A spacecraft's mission objective determines what flight requirements are needed to ensure mission success. These flight requirements are deceleration, heating, and impact and landing accuracy. A spacecraft must have maximum value of deceleration low enough to keep the weakest points of its vehicle intact but high enough to penetrate the atmosphere without rebounding. Spacecraft structure and payload mass affect how much maximum deceleration it can stand. This force is represented by "g's", or Earth's gravitational acceleration. If its structure is well-designed enough and made from robust material (such as steel), then it can withstand a higher amount of g's. However, payload needs to be considered. Just because the spacecraft's structure can withstand high g's does not mean its payload can. For example, a payload of astronauts can only withstand 12 g's, or 12 times their weight. Values that are more than this baseline will cause death. It must also be able to withstand high temperature caused by the immense friction resulting from entering the atmosphere at hypersonic speed. Finally, it must be able to penetrate an atmosphere and land on a terrain accurately, without missing its target. A more constricted landing area calls for more strict accuracy. In such cases, a spacecraft will be more streamlined and possess a steeper re-entry trajectory angle. These factors combine to affect the re-entry corridor, the area in which a spacecraft must travel in order to avoid burning up or rebounding out of an atmosphere. All of these above requirements are met through the consideration, design, and adjustment of a spacecraft's structure and trajectory.
The overall dynamics of aeroshells are influenced by inertial and drag forces, as defined it this equation: ß=m/CdA where m is defined as the mass of the aeroshell and its respective loads and CdA is defined as the amount of drag force an aeroshell can generate during a freestream condition. Overall, β is defined as mass divided by drag force (mas per unit drag area). A higher mass per unit drag area causes aeroshell entry, descent, and landing to happen at low and dense points of the atmosphere and also reduces the elevation capability and the timeline margin for landing. Factors that increase during EDL include heat load and rate, which causes the system to forcefully accommodate to the increase in thermal loads. This situation reduces the useful landed mass capability of entry, descent, and landing because an increase in thermal load leads to a heavier support structure and thermal protection system (TPS) of the aeroshell. Static stability also needs to be taken into consideration as it is necessary to maintain a high-drag altitude. This is why a swept aeroshell forebody as opposed to a blunt one is required; the previous shape ensures this factor’s existence but also reduces drag area. Thus, there is a resulting tradeoff between drag and stability that affects the design of an aeroshell’s shape . Lift-to-drag ratio is also another factor that needs to be considered. The ideal level for a lift-to-drag ration is at non-zero.[2]
Planetary Entry Parachute Program

NASA's Planetary Entry Parachute Program (PEPP) aeroshell, tested in 1966, was created to test parachutes for the Voyager Mars landing program. To simulate the thin Martian atmosphere, the parachute needed to be used at an altitude more than 160,000 feet above the Earth. A balloon launched from Roswell, New Mexico was used to initially lift the aeroshell. The balloon then drifted west to the White Sands Missile Range, where the vehicle was dropped and the engines beneath the vehicle boosted it to the required altitude, where the parachute was deployed.
The Voyager program was later canceled, replaced by the much smaller Viking program several years later. NASA reused the Voyager name for the Voyager 1 and Voyager 2 probes to the outer planets, which had nothing to do with the Mars Voyager program.
Low-Density Supersonic Decelerator
The Low-Density Supersonic Decelerator or LDSD is a space vehicle designed to create atmospheric drag in order to decelerate during entry through a planet's atmosphere.[3] It is essentially a disc-shaped vehicle containing an inflatable, doughnut-shaped balloon around the outside. The use of this type of system may allow an increase in the payload.
It is intended to be used to help a spacecraft decelerate before landing on Mars. This is done by inflating the balloon around the vehicle to increase the surface area and create atmospheric drag. After sufficient deceleration, a parachute on a long tether deploys to further slow the vehicle.
The vehicle is being developed and tested by NASA's Jet Propulsion Laboratory.[4] Mark Adler is the project manager.[5]
June 2014 test flight
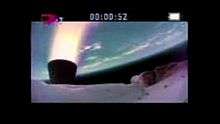
The test flight took place on June 28, 2014, with the test vehicle launching from the United States Navy's Pacific Missile Range Facility in Kauaʻi, Hawaiʻi, at 18:45 UTC (08:45 local).[5] A high-altitude helium balloon, which when fully inflated has a volume of 1,120,000 cubic meters (39,570,000 cu ft),[4] lifted the vehicle to around 37,000 meters (120,000 ft).[6] The vehicle detached at 21:05 UTC (11:05 local),[5] and four small, solid-fuel rocket motors spun up the vehicle to provide stability.[6]
A half second after spin-up, the vehicle's Star 48B solid-fuel motor ignited, powering the vehicle to Mach 4 and an altitude of approximately 55,000 meters (180,000 ft).[6] Immediately after rocket burn-out, four more rocket motors despun the vehicle.[4] Upon slowing to Mach 3.8, the 6-meter (20 ft) tube-shaped Supersonic Inflatable Aerodynamic Decelerator (SIAD-R configuration) deployed.[6] SIAD is intended to increase atmospheric drag on the vehicle by increasing the surface area of its leading side, thus increasing the rate of deceleration.[7]
Upon slowing to Mach 2.5 (around 107 seconds after SIAD deployment[4]), the Supersonic Disk Sail (SSDS) parachute was deployed to slow the vehicle further.[6] This parachute measures 33.5 meters (110 ft) in diameter, nearly twice as large as the one used for the Mars Science Laboratory mission.[8] However, it began tearing apart after deployment,[9] and the vehicle impacted the Pacific Ocean at 21:35 UTC (11:35 local) travelling 32 to 48 kilometers per hour (20 to 30 mph).[5][10] All hardware and data recorders were recovered.[7][10] Despite the parachute incident, the mission was declared a success; the primary goal was proving the flight worthiness of the test vehicle, while SIAD and SSDS were secondary experiments.[7]
2015 test flights
Two more test flights of LDSD will take place in mid-2015 at the Pacific Missile Range Facility. These will focus on the 8-meter (26 ft) SIAD-E and SSDS technologies, incorporating lessons learned during the 2014 test.[10] Changes planned for the parachute include a rounder shape and structural reinforcement.[9] Shortly after re-entry the parachute was torn away.[11]
Gallery
-
Artist impression of the Viking Orbiter releasing the aeroshell-clad lander (Don Davis).
-
Mars Science Laboratory giant heat shield.
-
Detail of Apollo 12 heat shield on display at the Virginia Air and Space Museum.
-
33.5-meter Supersonic Ring Sail Parachute
-
6-meter SIAD-R
-
8-meter SIAD-E
References
- ↑ "Returning from Space: Re-Entry" (PDF). Federal Aviation Administration. U.S. Department of Transportation. Retrieved 12 April 2015.
- ↑ "Hypersonic Entry Aeroshell Shape Optimization" (PDF). Solar System Exploration. NASA. Retrieved 12 April 2015.
- ↑ Erdman, Shelby Lin; Botelho, Greg (June 29, 2014). "NASA tests flying saucer craft for future manned mission to Mars". CNN.com. Retrieved August 12, 2014.
- 1 2 3 4 "Press Kit: Low-Density Supersonic Decelerator (LDSD)" (PDF). NASA.gov. May 2014. Retrieved August 12, 2014.
- 1 2 3 4 Carney, Emily (July 1, 2014). "NASA's Low-Density Supersonic Decelerator Test Flight Hailed as a Success". AmericaSpace. Retrieved August 12, 2014.
- 1 2 3 4 5 Parslow, Matthew (June 28, 2014). "LDSD passes primary technology test but suffers chute failure". NASA Spaceflight. Retrieved August 12, 2014.
- 1 2 3 McKinnon, Mika (June 29, 2014). "A Successful First Flight for of the Saucer Test Vehicle over Hawaii". io9.com. Retrieved August 12, 2014.
- ↑ Chang, Alicia (June 1, 2014). "NASA to test giant Mars parachute on Earth". Las Vegas Review-Journal. Associated Press. Retrieved August 12, 2014.
- 1 2 Boyle, Alan (August 8, 2014). "Flying Saucer Videos Reveal What Worked and What Didn't". NBC News. Retrieved August 12, 2014.
- 1 2 3 Rosen, Julia (June 30, 2014). "NASA Mars test a success. Now to master the parachute". Los Angeles Times. Retrieved August 12, 2014.
- ↑ Allman, Tim (June 9, 2015). "Parachute on Nasa 'flying saucer' fails in test". BBC. Retrieved June 9, 2015.
- "Lockheed Martin To Design Mars Science Lab Aeroshell". Mars Daily. 2006-03-30. Retrieved 2007-02-17.
"For Fuel Conservation in Space, NASA Engineers Prescribe Aerocapture". NASA. 2006-08-17. Retrieved 2007-02-17.
- Space travel guide
- Early Reentry Vehicles: Blunt Bodies and Ablatives
- Axdahl, Erik; Cruz, Juan R.; Schoenenberger, Mark; Wilhite, Alan. "Flight Dynamics of an Aeroshell Using an Attached Inflatable Aerodynamic Decelerator" (PDF). NASA.gov. American Institute of Aeronautics and Astronautics. Retrieved 12 April 2015.