Acheson process
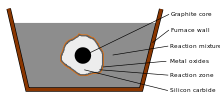
The Acheson process is a process to synthesize graphite and silicon carbide, named after its inventor Edward Goodrich Acheson.
The process consists of heating a mixture of silica or quartz sand[1] and powdered coke (carbon) in an iron bowl. Acheson, in 1890, originally attempted to synthesize artificial diamond, but ended up creating blue crystals of silicon carbide, which he called carborundum.[2] When heated the silicon is removed, leaving graphite. The process was patented by Acheson in 1896.[3] After discovering this process, Acheson developed an efficient electric furnace based on resistive heating, the design of which is the basis of most silicon carbide manufacturing today. Silicon carbide was a useful material in jewelry making due to its abrasive properties, and this was the first commercial application of the Acheson process.[4]
In the furnace, an electric current was passed through a graphite core, surrounded by sand, salt, and carbon. The electric current heated the graphite and other materials, allowing them to react, producing a layer of silicon carbide around the graphite core. The process gives off carbon monoxide. There are four chemical reactions in the process that produces silicon carbide (SiC):[4]
- C + SiO2 → SiO + CO
- SiO2 + CO → SiO + CO2
- C + CO2 → 2CO
- 2C + SiO → SiC + CO
The first light emitting diodes were produced using silicon carbide from the Acheson process. The potential use of silicon carbide as a semiconductor led to the development of the Lely process, which was based on the Acheson process, but allowed control over the purity of the silicon carbide crystals.[5]
The first commercial plant using the Acheson process was built by Acheson in Niagara Falls, New York, where hydroelectric plants nearby could cheaply produce the necessary power for the energy intensive process. By 1896, The Carborundum Company was producing 1 million pounds of "carborundum".[6] Many current silicon carbide plants use the same basic design as the first Acheson plant. In the first plant, sawdust and salt were added to the sand to control purity. The addition of salt was stopped in the 1960s, as the advantages of greater purity were outweighed by the disadvantages of the corrosion of steel structures, which the salt caused. The addition of sawdust was stopped in some plants to reduce emissions.[4]
In the manufacture of synthetic graphite, the Acheson process is run for approximately 20 hours, with currents of 200 A, and voltages of 40,000–50,000 V (8–10 MW). The purity of graphite achievable using the process is 99.5%.[7]
References
- ↑ "The Art of Silicon Carbide". www.sic.saint-gobain.com. Retrieved 2015-10-22.
- ↑ Mary Bellis (2013-07-19). "Edward Goodrich Acheson – Carborundum". Inventors.about.com. Retrieved 2013-08-22.
- ↑ "Manufacture of graphite". United States Patent Office. 1896-09-29. Retrieved 2011-12-05.
- 1 2 3 Weimer, A.W. (1997). Carbide, Nitride and Boride Materials Synthesis and Processing. London: Chapman & Hall. pp. 115–122. ISBN 0-412-54060-6.
- ↑ Saddow, S.E. (2004). Advances in silicon carbide processing and applications. Norwood, Massachusetts: Artech House. pp. 4–6. ISBN 1-58053-740-5.
- ↑ "Minor Paragraphs". Popular science monthly: 431. Jan 1898. Retrieved 13 May 2013.
- ↑ Erwin, D.L. (2002). Industrial Chemical Process Design. New York: McGraw-Hill. p. 579. ISBN 0-07-137620-8.
Further reading
- Cardarelli, François (2008-01-09). Materials handbook: A concise desktop reference. ISBN 978-1-84628-668-1.
- Zetterling, Carl-Mikael; Engineers, Institution of Electrical (2002-11-01). Process technology for silicon carbide devices. ISBN 978-0-85296-998-4.
- Erwin, Douglas (2002-05-17). Industrial chemical process design. ISBN 978-0-07-137621-1.
- Gupta, G. S.; Vasanth Kumar, P.; Rudolph, V. R.; Gupta, M. (2001). "Heat-transfer model for the acheson process". Metallurgical and Materials Transactions A. 32 (6): 1301. doi:10.1007/s11661-001-0220-9.